Plate & Frame
Heat Exchanger.
Advantages of a PHE
Small Footprint
Service Accessibility
Efficiency
Fluid Compatibility
Versatile Design
Expandable Design
Disdvantages of a PHE
-
ContaminationOver time plates will build up with scale and debris
-
ReplacementGaskets tend to leak overtime, typically after 10-15 years replacements are required depending on the application
-
ApplicationNot compatible for higher temperatures and pressures
Main Components of a PHE
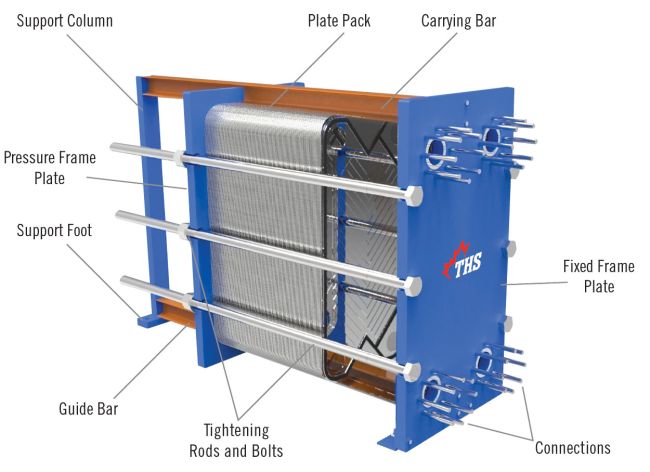
Main Components of a Plate
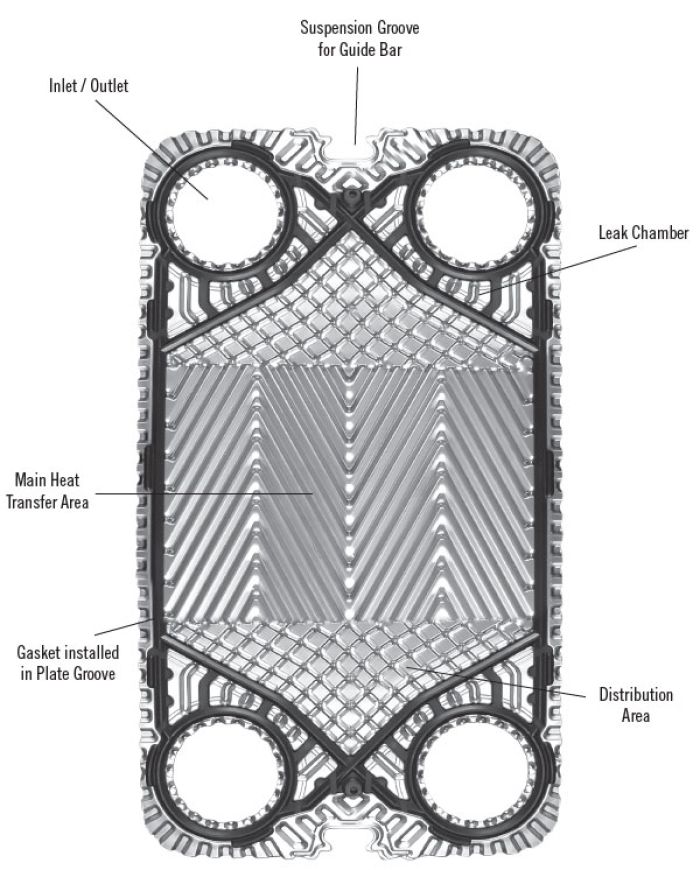
Applications
Food & Beverage
Sterilization
Evaporation
UHT Treatment
Reception Thermization
Wort Boiling
Industrial
Demineralization
Evaporation
Economizing
Heat Recovery
Quench Oil Cooling
Caustic Solution Heating
Energy
Geothermal
Quench Coolers
Lubrication Oil Cooling
Corrosive Fluid Heating/Cooling
Crude Oil Heating
Diesel Engine Cooling
Auxiliary Cooling
Chemical & Pharmaceutical
Glycol Cooling
Reactor Cooling
Extraction
Fermentation
Fragmentation
Methanation
Commercial HVAC
Swimming Pool Heating
Free Cooling
Cooling Tower Isolation
Heat Pump Systems
Heat Recovery
Thermal Storage Systems
Marine
Auxiliary Power Generation System
Jacket Water Cooling
Central Cooling
Seawater Isolation Exchanger
Engine Oil Cooling
Ventilation Coolers and Heaters
When Should A Plate & Frame Heat Exchanger Be Serviced?
As a heat exchanger becomes fouled with dirt, debris or scale often the modulating valve provides additional hot or cold liquid to help compensate for the loss of efficiency of the heat exchanger.
Over time the control valve will continue to open fully. Unfortunately on the hottest or coldest days, even with the valve fully open the heat exchanger cannot meet the thermal transfer requirements and the situation becomes critical.
Monitoring just the operating temperature provides a false sense of security. Recording the difference in the outlet and inlet pressures provides a more accurate result of the amount of fouling.
Fouling equal to the thickness of a piece of paper represents a 20% loss of thermal efficiency. In addition, the energy cost for pumps increases since the pump must work harder to overcome the increased pressure resistance through the PHE.
Differential pressure average for a PHE equals 2-4 psi when equipped with new or refurbished plates;
Service should be scheduled when the differential pressure increases up to 7-10 psi.
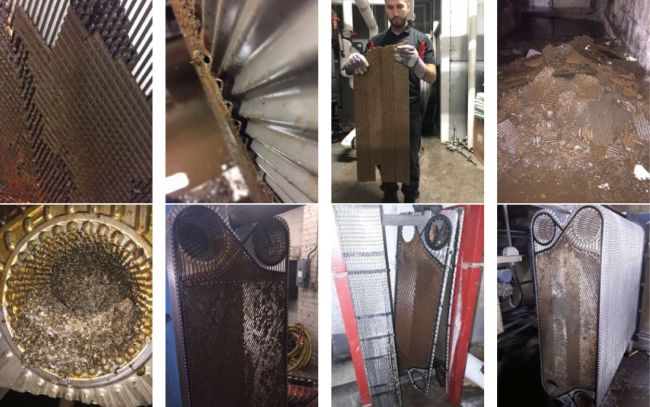
Fouled Plates Requiring Service or Replacement
What Causes Plate & Frame Heat Exchangers To Leak Internally?
- Higher pressure side will leak into the lower pressure side, if a plate develops a pin hole or crack;
- Over time the plates can crack since they are continuously flexing, this is often referred to as a “pop can effect” - continually bending the can back and forth in the same area will break it apart;
- Cross contamination is preventable when “double walled” designed plates are used with potable water.
*Municipal codes verify from region to region with most new construction by-laws requiring this safety measure

Damaged Plates
What Causes Plate & Frame Heat Exchangers To Leak Externally?
- Rubber gaskets installed on each plate create a seal, when gaskets become worn or damaged
- As the PHE ages the gaskets can dry out, lose their elasticity and become brittle
- Operating temperatures, pressures and exposure to process fluids can all reduce the life of a gasket
- Spiking or water hammer can force a gasket out of the plate groove
- Overheating can melt the rubber and cause the gasket to become brittle and crack
- Over tightening the groove the gasket sits in can become deformed. When this occurs the gasket will not sit flat and pushes outwards, (.4)mm thick gaskets are very susceptible to this issue
- Plates not installed correctly in a honeycomb pattern
The life span of a gasket in a cooling application is 10-15 years and for a heating application 8-10 years. Gaskets exposed to steam will typically wear quicker than if exposed to boiler water. PHE’s used strictly for seasonal heating will often leak during the first month of startup and seal after a few weeks as the gaskets expand.
When plates are installed correctly they will form a honeycomb pattern and if glue-less gaskets such as clip or ball are used, the tabs will be aligned.
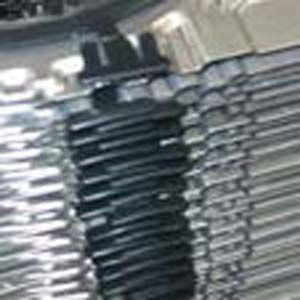
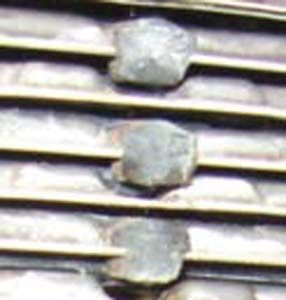
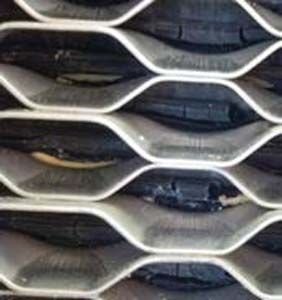
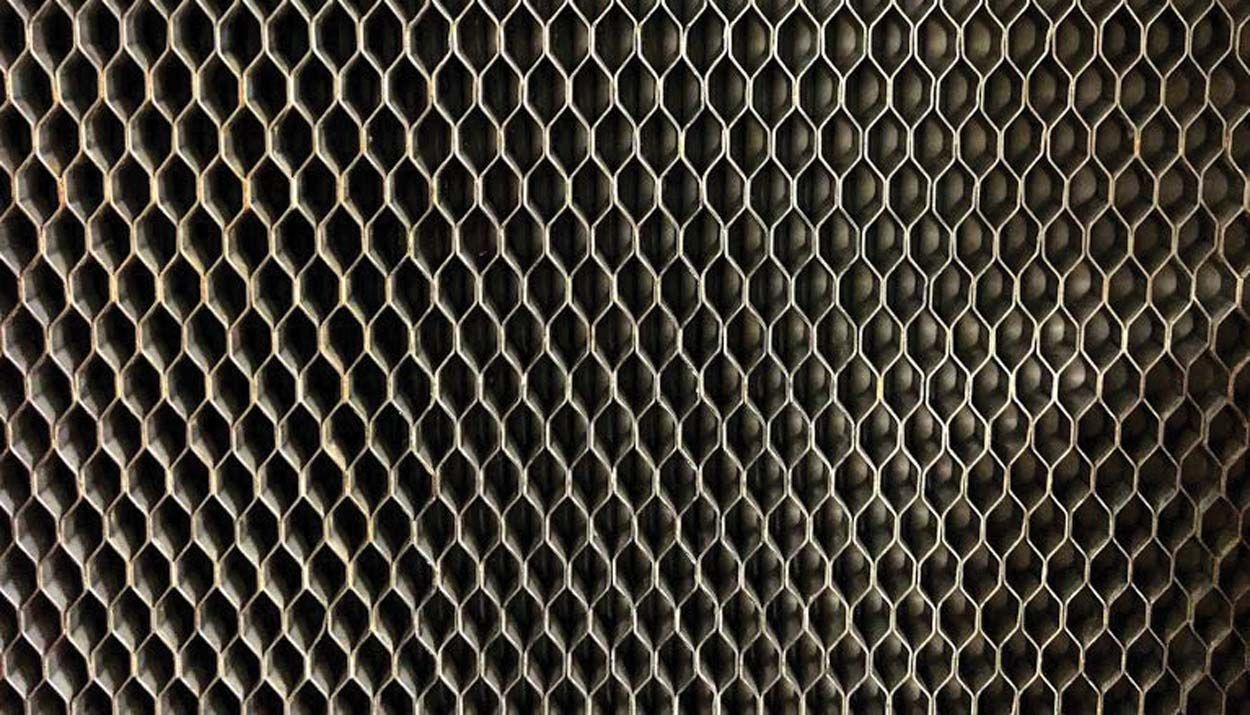
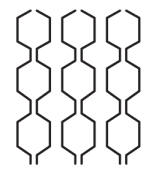
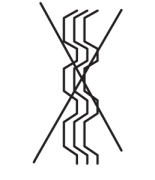